電動汽車(EV)的市場份額迅速增加,2023年,預計新能源產銷將超過900萬輛,2024年,業內預計新能源汽車批發輛將達到1100萬輛,滲透率將會達到40%。展望未來,電動汽車市場將趨於平穩還是繼續上漲?
我們正面臨著汽車架構領域千載難逢的行業範式轉變。如果製造商能夠更高效地設計和生產電動汽車,同時集中整合電子組件的占位面積,並且成本比當前的模式便宜,那麼電動汽車市場將繼續上升。在本文中,我們將探討電動汽車行業在多個層面上實現這些目標。
更高效的充電
緩解電動汽車的主要痛點
一輛傳統燃油車只需花費大約五分鐘的時間加油,駕駛員已經習慣了很快便可以重新上路的體驗。公共的電動汽車充電站能否實現類似的充電時間?
據中國電動汽車充電基礎設施促進聯盟發布的數據顯示,截至2023年11月,我國充電基礎設施保有量達到了826.4萬台,同比增長了67.0%。其中,公共充電基礎設施保有量達到了262.6萬台,同比增長了51.7%;私人充電基礎設施保有量為563.8萬台,同比增長了75.2%。公共充電站的技術進步允許更快充電功率和速度。更好的充電技術增加了對電動汽車的電力輸送,為車輛提供更多電力,並且減少充電時間。
電動汽車充電基礎設施在電力容量方面有所改善。具有更高功率輸出的快速充電器,例如DC快速充電器,現在也更為普遍。這些充電器可以為車輛提供更多的電力,從而為時間緊迫的駕駛者提供更高效的充電操作。
越來越多的充電站現在還具有動態充電功能,允許根據電池的充電狀態調整功率。這種動態充電功能可確保電池始終獲得最佳充電速率,從而最大限度地提高充電效率和縮短充電時間。
更小、更輕的組件全面節省成本
在整個電子系統中減少組件的占位面積並減輕重量,這在提高電動汽車的效率和成本效益方面發揮著關鍵作用。
較小的封裝尺寸
當空間非常寶貴時,小型化有助於最大限度地提高性能。將所有電子組件安裝到電動汽車中是複雜的操作,設計工程師正在尋找促使電子組件更加緊湊的方法。線束封裝由導線尺寸和電壓推動發展,通過減小線束尺寸和提高效率,可以減輕車輛的總體重量。
減輕重量
雖然相比傳統的銅線更厚,但鋁電纜有助於減輕重量和節省成本。而且,儘管需要更大規格的導線來傳導同樣的電能,但鋁線的重量僅為銅線重量的30%。此外,鋁線的成本最高僅為銅線的一半。
製造商已經開始使用金屬合金、複合材料和聚合物來進一步減輕內部電子系統的重量。使用這些材料可以在不影響功能性和耐用性的情況下減輕車輛的重量。
綜合效能
通過減小重量和封裝尺寸,並在適當的情況下選擇成本效益更高的材料,電動汽車可以在不犧牲性能的情況下提高效率。優化整個車輛裝配中的每個組件,這些價值能夠帶來實際的效率提升。
降低系統溫度是安全高效電動汽車的關鍵
設計工程師正在努力降低電氣系統的溫度。例如,電動汽車中使用的連接器優化後能適應較低的溫度,允許使用成本較低的樹脂而不影響性能。這種優化消除了連接器的過度工程設計,從而降低成本,同時保持可靠性和功能性。
占位面積較小且產生熱量較少的電子組件,允許實現更好的散熱。散熱片使用具有高導熱性的材料,吸收和消散由電氣組件產生的熱量。絕緣技術亦幫助減少EV內部冷熱區域之間的熱傳遞。這可以防止熱降解,使得每個系統都能按設計運行。結合這些散熱技術,EV內部組件能夠承受高運作溫度,而不會影響性能。
先進電池管理系統提高EV整體效率
電動汽車的電池管理系統(BMS)採用各種控制技術,如充放電控制、溫度調節和監測電池電位、電流和電壓,在監控電池存儲系統方面發揮著至關重要的作用。這些技術措施確保進行適當的監控及持續監控,從而有效地提升能源管理系統(EMS)的安全性及使用壽命。
通過結合電池充電狀態的準確性、電池平衡、散熱管理和防止過度充電和放電,先進的BMS幫助整個車輛有效地分配和優化能源水平。在Molex莫仕最近針對800多名設計工程師進行的調研中,22%的受訪人士表示,電池組是設計或實施電動汽車動力系統時的最大挑戰,它被列為僅次於車載電力電子的第二大難題。
設計人員正採用更高的電壓電源,使用48V電壓替代12V電壓來連接驅動傳感器、電機、ECU和其他組件。更高的電壓以更少的電流提供相同的能量,允許採用更薄、更輕的電纜。同樣,電動汽車動力系統正在轉向更高電壓的架構,並採用更高效的控制器和布線設置。
Molex莫仕出品的Volfinity電池連接系統,具有可靠且易於使用的特性,可以將電池連接到電動汽車電池模塊的控制板上,不再需要菊花鏈電線連接。藉助該總體解決方案可以整合電池傳感功能、電池監控與平衡以及溫度測量功能,已在多款產品上驗證並獲得市場認可。
▲Volfinity 電池連接系統
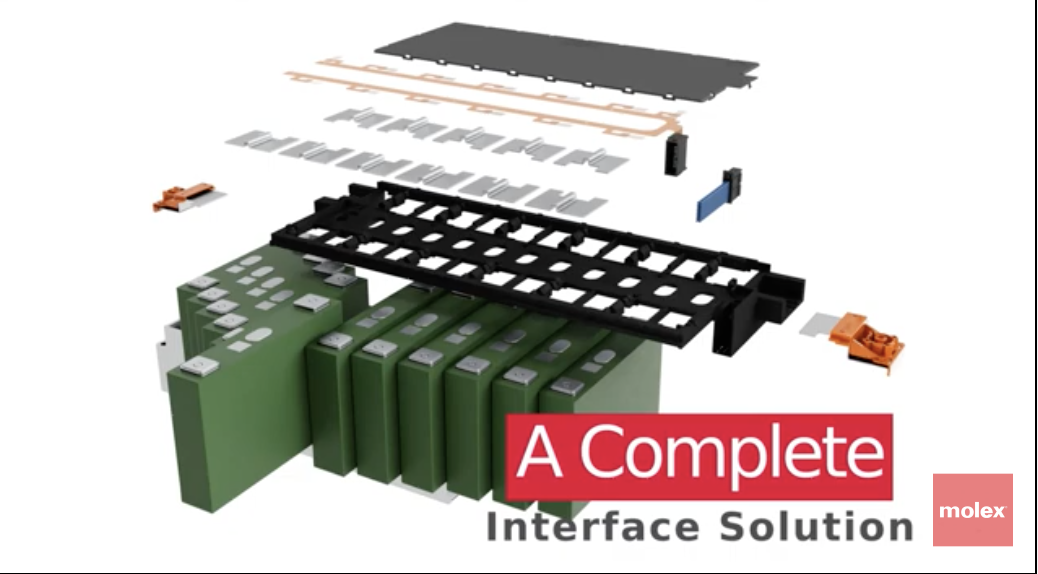

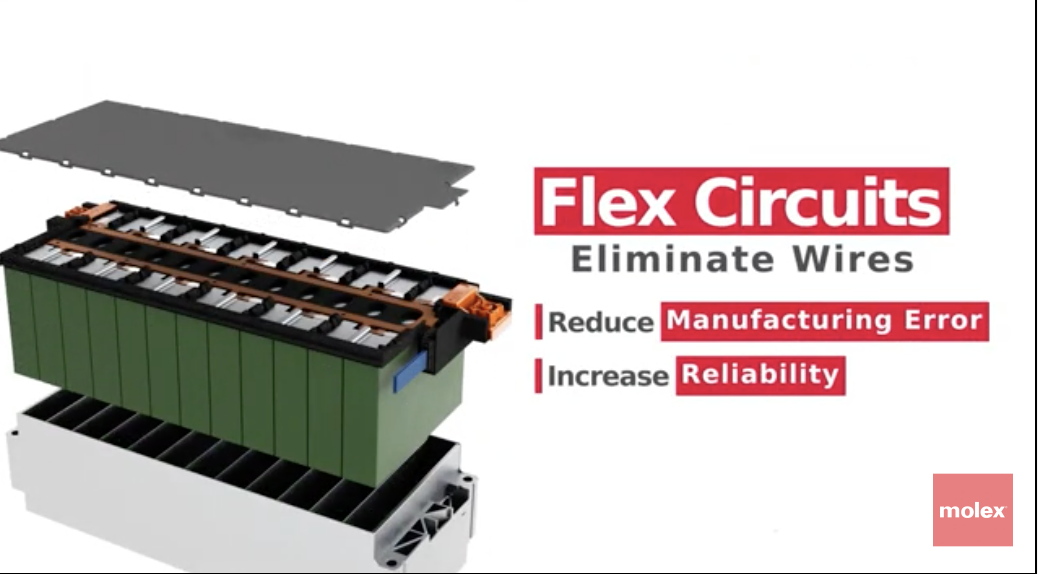
Volfinity產品細節
推動電動汽車的未來發展
以上討論到的技術改進,使得電動汽車可以使用更緊湊、重量更輕的電子組件,從而提高車輛效率,助力電動汽車行業開啟下一個精彩篇章。
評論